Verdens største kjølesenter for sjømat – The World Seafood Center
For drøyt ett år siden, 3.januar 2022, ble første spadetak tatt for det som skal bli kanskje verdens største kjølesenter for sjømat. For OAC Logistics AS, med leietakerne Gardermoen Perishable Center, Oslo Seafood Center og Mowi er Vedal nå godt i gang med The World Seafood Center (WSC).
Fremtidsrettet og moderne
Sjømatlageret på ca. 55 000 kvadratmeter vil ha de mest moderne løsningene for å dekke fremtidens behov for eksport av fersk, norsk sjømat til Europa og resten av verdensmarkedet. En betydelig del av all laks som eksporteres ut av Norge vil gå gjennom dette anlegget. Eksporten av sjømat har som mål å dobles fra 2020 til 2030, og femdobles innen 2050. Dette bygget vil være en viktig bidragsyter for å nå disse målsetningen. Prosjektet gjennomføres med en ambisiøs miljøstrategi og Breeam-sertifisering.
Konkrete, miljøbesparende tiltak
I Vedal skal vi tilby bransjeledende miljøkompetanse. Et av målene våre er å redusere mengden avfall og legge til rette for at materialene får så lang levetid som mulig.
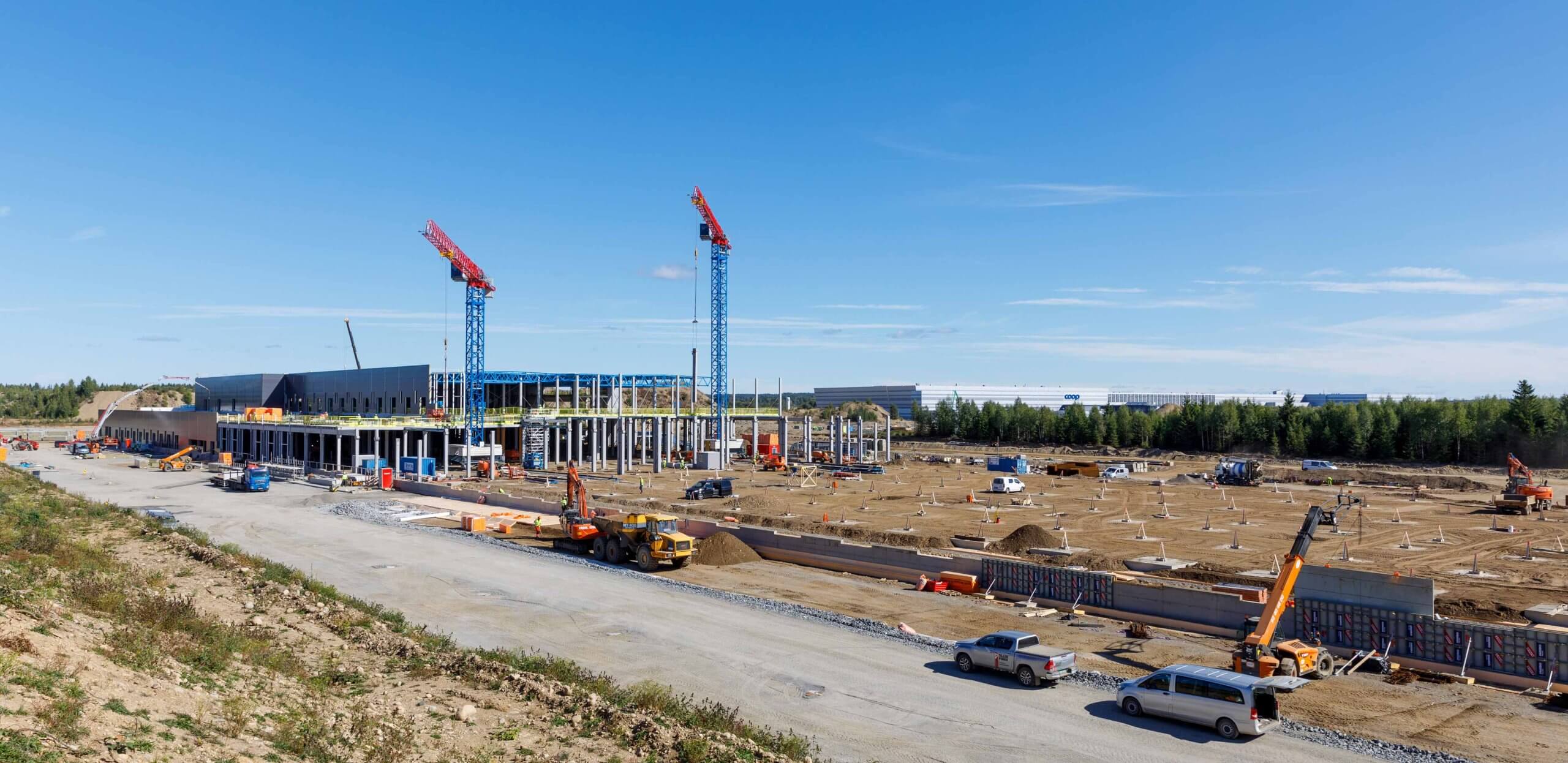
Ved sjømatlageret benytter man seg av to skinnegående kraner for prefabrikkert montasje. Etter erfaringer man gjorde seg fra det første byggetrinnet, hvor man benyttet seg av stripefundamentering, så man på alternativer til kranfundament for byggetrinn 2. Løsningen ble leie av stålplater fra Stavdal, som kan leveres tilbake når prosjektet er ferdig med dem. Bruk av stålplater og etappevis flytting av disse krevde mer nøyaktig avretting og noen flere administrasjonstimer sammenlignet med kontinuerlig stripefundamenter, men tidsforbruket er fortsatt i favør av stålplater. Tiltaket viste å gi stor gevinst – både miljømessig og økonomisk.
Estimater viser at leie av stålplater er omtrent 10 % billigere enn å støpe betong. Den største gevinsten ved tiltaket er allikevel materialbesparelse og reduksjon av direkte, umiddelbare klimagassutslipp. Stripefundamentene langs BT1 resulterte i utslipp av omtrent 70 000 kg CO2e. Ved bruk av stålplater i BT2, som var noe kortere enn BT1, var man til sammenligning nede i 13 000kg CO2e. I Norge slipper man ut ca. 7 600 kg CO2 per innbygger per år.
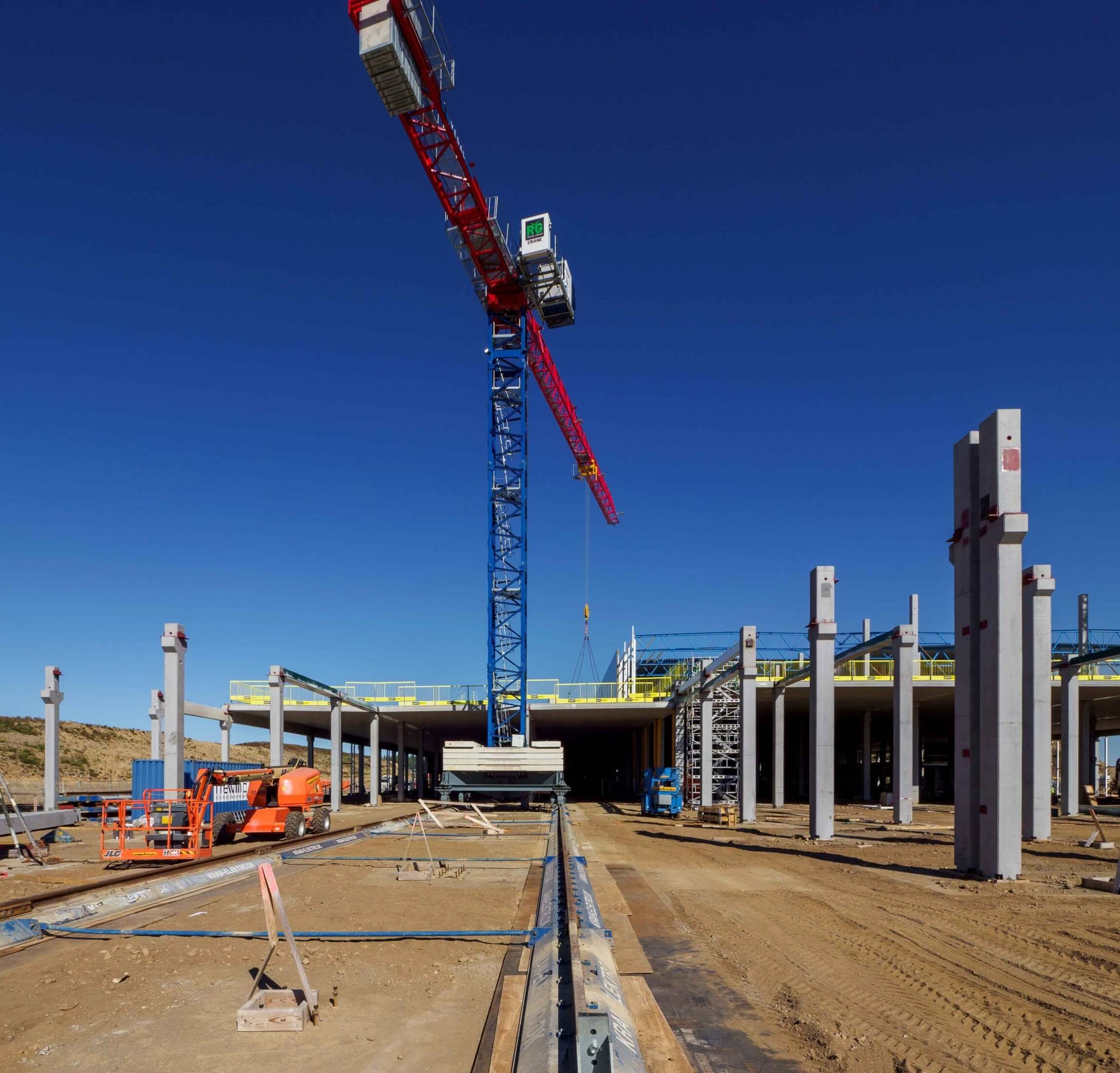
Redusert fotavtrykk og arealbesparelser
Sjømatlageret bygges i to etasjer, med ramper for tungtransport som leder vei til taket av plan 1. Logistikkbygg har historisk stort sett blitt bygd kun over ett plan med en utnyttelse på mellom 40 til 50%. På WSC reduserer man byggets fotavtrykk og utnytter arealet bedre med en utnyttelse på over 80%, noe som også fører til et mindre inngrep i naturen. Det forutsetter større dimensjoner på fundamentene, men med det samme taket, de samme veiene rundt og den samme VA-infrastrukturen har dette en positiv effekt på miljøet. Det er effektivt å bygge i høyden rundt knutepunkter, og når sjømatlageret står ferdig vil det bidra til å redusere transportbehovet til og fra Gardermoen.
Gjenbruk og redusert avfall
I teorien er sjømatlageret et demonterbart bygg. Stort sett hele bygget baseres på prefabrikkerte elementer, noe som er med på å redusere avfallsmengden betraktelig. De aller største bygningselementene slik som fundamentarmering, bæresystem, takplater og sandwichelementer kommer til byggeplassen prefabrikkert. For å holde bygget innenfor områdets regulerte gesimshøyde har man kappet sandwichelementene. Avkappet gjenbrukes som klimaskiller mellom kalde og varme arealer innvendig i bygget.
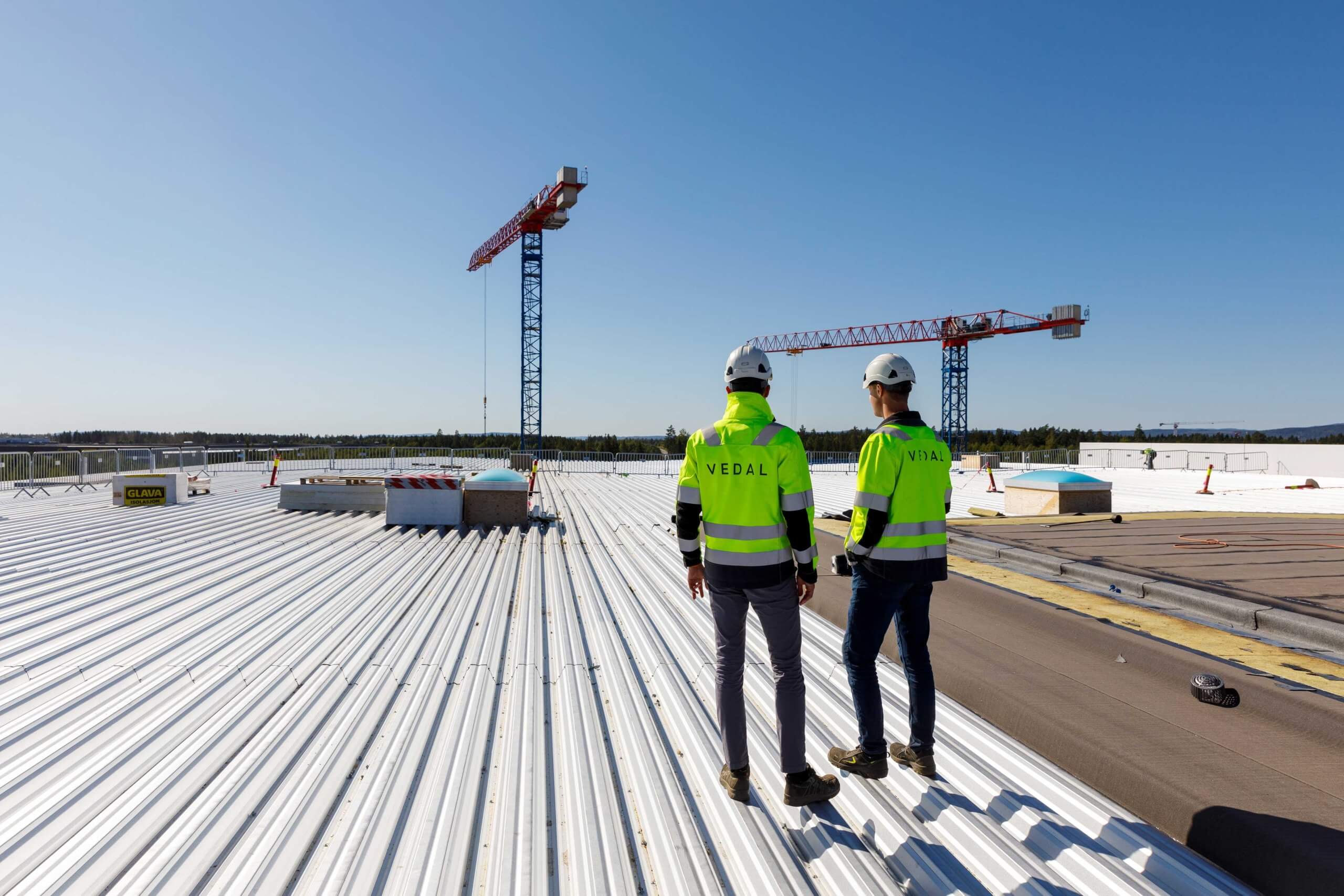
– Det er motiverende og inspirerende når man kan finne så konkrete tiltak som i tillegg til å være økonomisk gunstig for prosjektet gir en så tydelig klimagevinst. Vi har en fremoverlent Byggeherre i Oslo Airport City, som hele tiden pusher oss og samtidig gir oss spillerom til å finne de beste løsningene sammen med de andre gode samarbeidspartnerne vi har på prosjektet, sier prosjektleder Ola Samdal i Vedal Entreprenør.
Miljøvennlig transport
Gjennom hele byggeprosessen har de ansatte i Vedal tilbud om miljøvennlig transport mellom hjemsted og arbeidsplass ved bruk av kollektivtransport. For å forenkle reiseveien har man gått til innkjøp av en elektrisk minibuss som bringer og henter fra togstasjonen til byggeplassen hver eneste dag. Det er også etablert el-billadere på hele brakkeriggen.
Det er motiverende og inspirerende når man kan finne så konkrete tiltak som (...) gir en så tydelig klimagevinst.
The World Seafood Center
Bygget har flater på om lag 65 000 m2 og en byggetid på 23 måneder. Det er moreneavsetninger i grunnen i næringsparken. Bygget er direktefundamentert på disse etter en større utgraving. Graveplanen er omforent med myndigheter for å ikke bygge inn de store natursandressursene i området. All massetransport er kortreist; det etableres voller for turveier i nærområdet og sand leveres til nabovirksomheter. Det er også prosjektert frem løsning for naturlig overvannshåndtering på tomten.
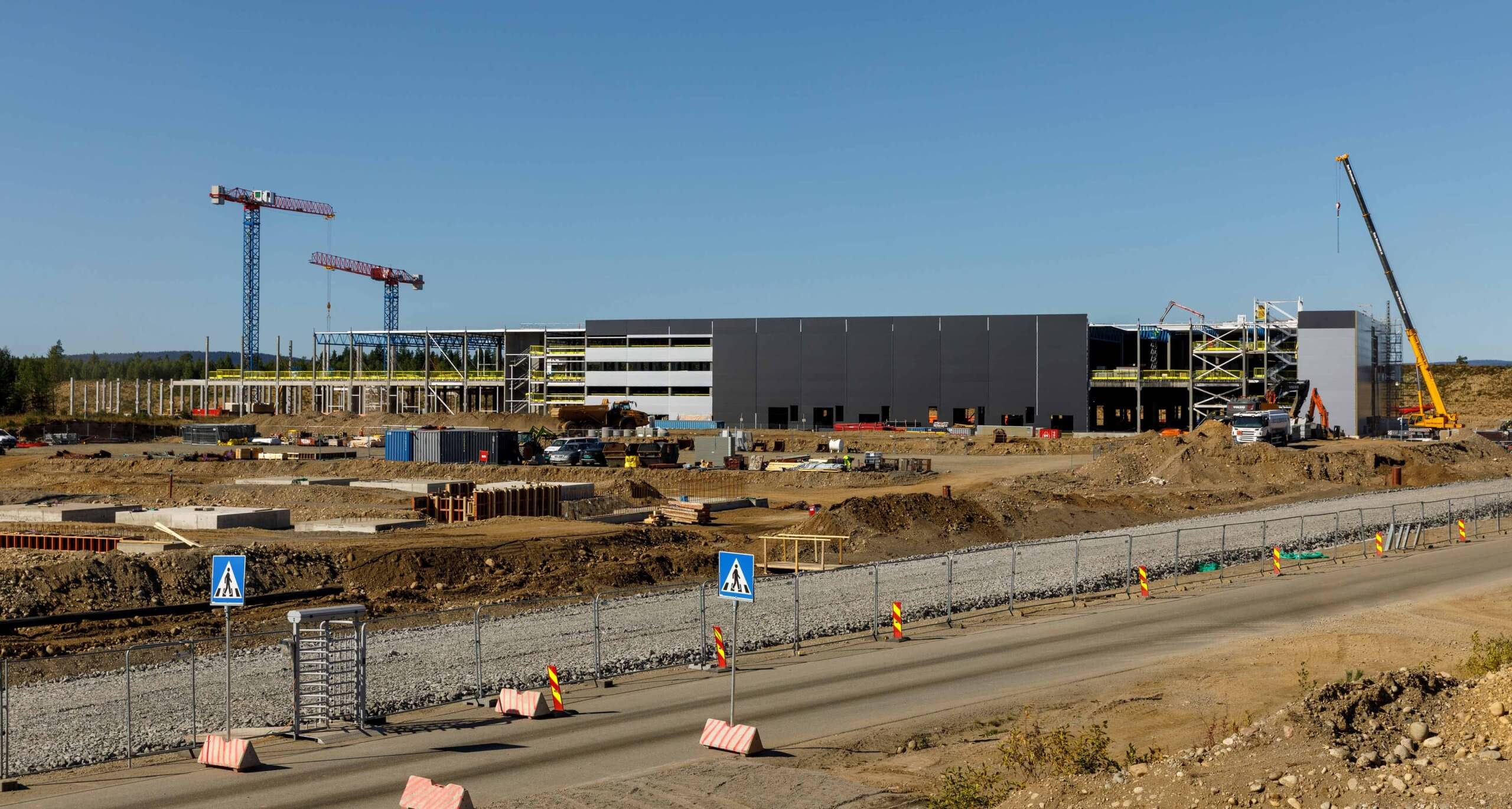
Fremdriftstakten er styrt av de to skinnegående tårnkranene. Disse flyttes ca. 20 meter annenhver uke. Det vil si at råbygg, tak og fasader følger denne takten. I snitt må det produseres om lag 80 centimeter ferdig bygg per arbeidsdag for å nå sluttdatoen.
Det tette samarbeidet og dialogen på tvers av alle involverte har bidratt til de gode løsningene og kvalitet i alle ledd.
Utvendige flater ble asfaltert 10 måneder etter byggestart. Dette utgjør store arealer med et omfattende VA-anlegg. Flatene legger til rette for god logistikk, noe som er sentralt for å kunne omsette i dette tempoet.
– Flere av prosjektets underentreprenører er lokale aktører. Rasjonelle produksjonsmetoder utarbeidet i samråd med underentreprenører og rådgivere står høyt i prosjektet. Det tette samarbeidet og dialogen på tvers av alle involverte har bidratt til de gode løsningene og kvalitet i alle ledd, sier Samdal.
Leietakere
Gardermoen Perishable Center (GPC) er en av de store aktørene innen distribusjon av sjømat som flyfrakt til destinasjoner over hele verden. GPC utvider nå satsningen sin i forbindelse med flytting til WSC. Oslo Seafood Center håndterer omlast, lagring, plukk m.m. av sjømat på kjøl og frys for sine kunder. Norske Mowi er verdens største oppdrettsselskap, og kontrollerer hele verdikjeden fra fôrproduksjon til stamfisk, rogn, matfisk, foredling og salg. Det meste av produksjonen eksporteres til Europa, USA og Asia. Mowi flytter nå sin fraktterminal til WSC, som vil bli deres knutepunkt for transport av laks som produseres i Norge.
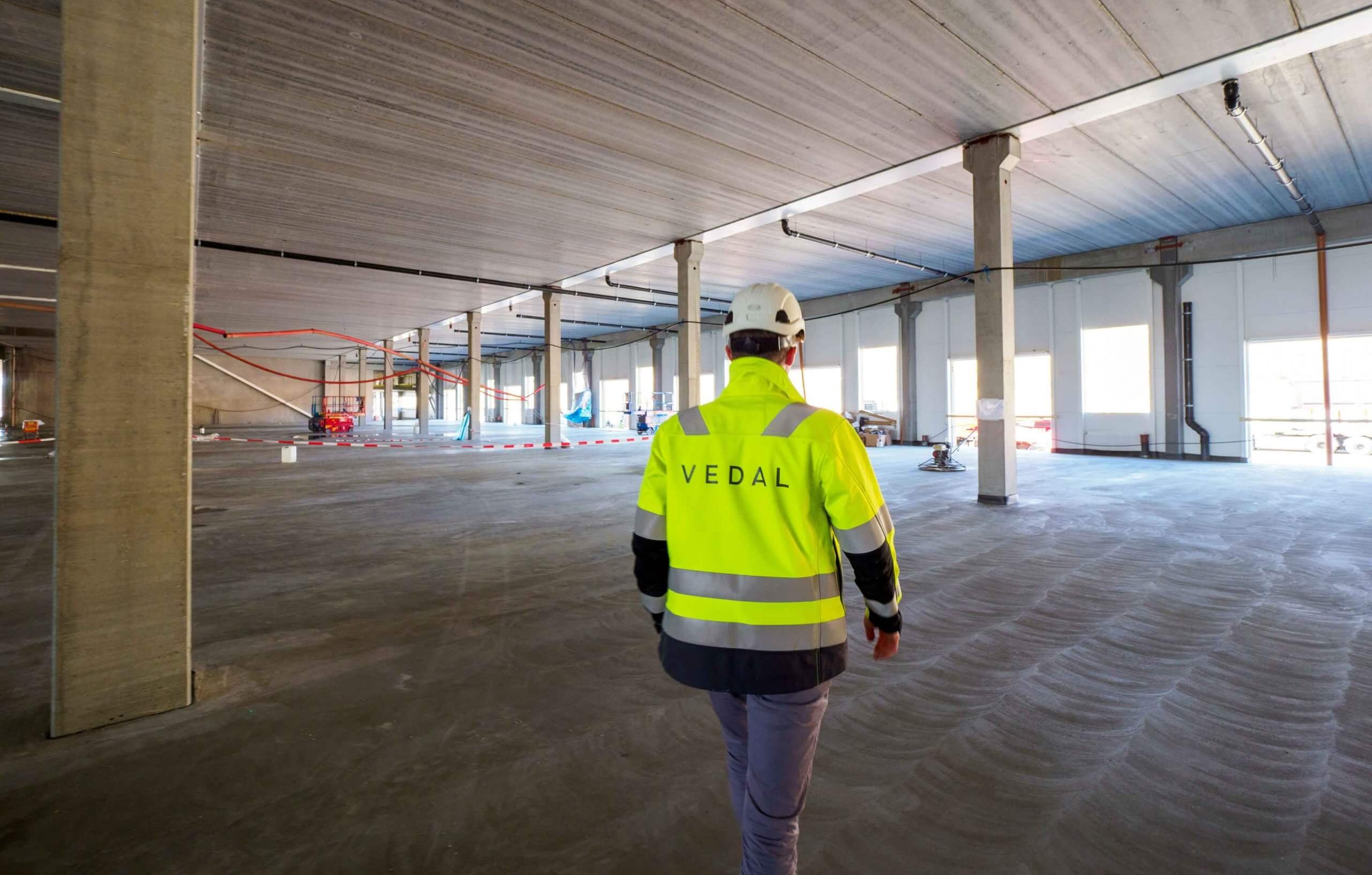
Logistikkanlegg og arbeidsplasser
Oslo Airport City er et område på 1150 mål i Gardermoen Næringspark. Dette har et utviklingspotensial på nesten én million utleibare kvadratmeter, og representerer et av de største utviklingsprosjektene i Norden. Utviklingen og byggingen vil trolig ta 30 år å ferdigstille, men etter hvert vil dette bli arbeidsplassen til ca. 20 000 mennesker. Sjømatlageret vil gi 300–400 arbeidsplasser til Ullensaker kommune. Den første fiskekassen vil bli ekspedert gjennom det enorme anlegget allerede sommeren 2023.
I tillegg til sjømatlageret har Vedal ferdigstilt Porsche Center Gardermoen, den første Breeam-sertifiserte bilbutikken i Norge, og er samtidig godt i gang med et spesiallogistikkanlegg på 15.000m2 som startet opp 1. august 2022.
Nysgjerrig på Oslo Airport City? Les mer om prosjektet her
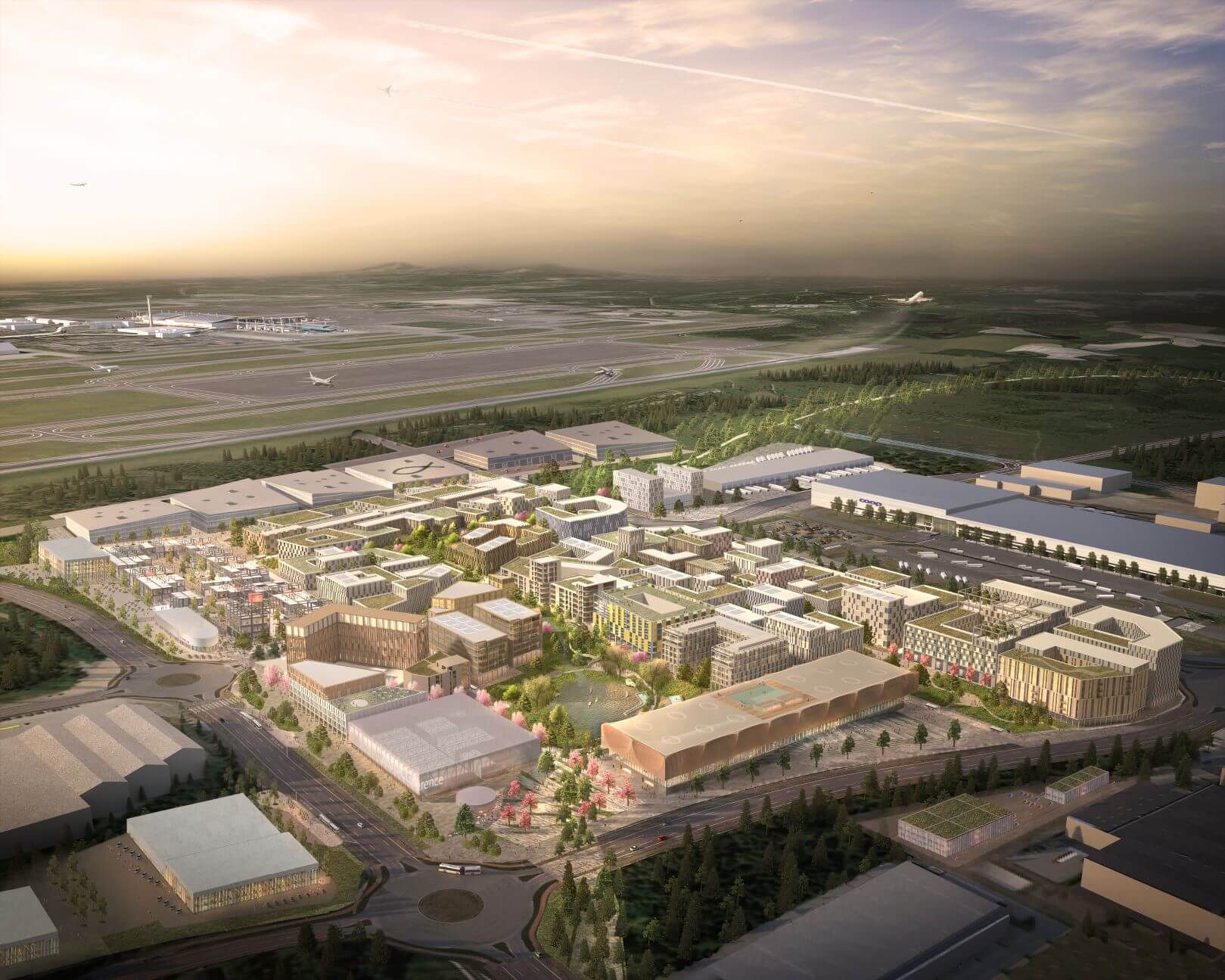